What are some tips for using a metal cutting saw?
Setting up your metal cutting saw
As a metal cutter, you are likely to use a number of different tools and machines throughout your work. One of these is the metal cutting saw. Setting up your saw correctly is essential for accurate and safe cutting.
There are a few things to keep in mind when setting up your saw. First, make sure the blade is properly aligned with the wheel or blade guard. Second, make sure the saw is positioned so that the blade will be at the correct height when cutting. Third, make sure the saw is level so that cuts are accurate. Finally, use safety precautions such as wearing protective gear and using an approved guard system
The Right Metal Cutting Saw for My Project
Choosing the right metal cutting saw for your project is essential to accuracy and efficiency. When looking for a saw, there are a few factors to consider. These include blade type, size and weight, motor power, and guard type.
Blade type is the most important consideration when choosing a metal cutting saw. Different blades are designed for different applications and each has its own advantages and disadvantages. For example, semi-finite blades are good for general purpose cutting while teeth-style blades are best suited for precision work. Size also matters when choosing a saw. The bigger the blade, the more torque it can generate, which is important if you plan on working with heavy materials or if you need to make multiple cuts quickly. Finally, weight is an important factor to consider when selecting a metal cutting saw because it will affect how easy it is to hold and control. A heavy saw will be easier to use than one that is too light, but one that is too heavy may be difficult to move around or even cause arm fatigue.
Motor power also plays an important role in selecting the right metal cutting saw for your project. A powerful motor allows you to make fast cuts without having to exert too much effort, making it easier to handle larger blades and heavier materials. Guard types also vary in terms of how they affect usability and performance. For example, offset guards allow you more flexibility in positioning the blade while miter gauges help ensure accurate cuts by measuring the angle at which the blade meets the wood surface
Cutting with your metal cutting saw
Metal cutting saws are one of the most important tools in a metalworker’s arsenal. They can be used for a variety of tasks, from simple cuts to intricate shaping. When using a metal cutting saw, it is important to follow proper safety guidelines.
One of the most important things to remember when using a metal cutting saw is to always wear safety gear. This includes a safety helmet, eye protection, and heavy duty gloves. It is also important to keep your hands well-protected; use protective sleeves and guards if necessary.
When making cuts with your metal cutting saw, it is important to be accurate. If you make too many mistakes, your project may end up ruined. To ensure accuracy, use a ruler and protractor to measure your cuts before making them. Additionally, use the blade depth gauge on your tool to ensure that you are making the correct depth cuts.
Finally, always take care when moving or handling your metal Cutting Saw after use. Be sure to unplug it before taking it apart or cleaning it – otherwise you could create sparks that could start a fire.
Maintaining your metal cutting saw
One of the most important aspects of maintaining a metal cutting saw is keeping it clean. If the blade is dirty, it will not perform as well and may even cause damage to the saw. Cleaning the blade includes using a brush to remove any dust or debris, then using a solvent or cleaning solution to completely sanitize the blade. After sanitizing, make sure to dry the blade thoroughly with a cloth before storing it.
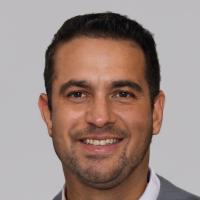
Mike Fleming
Mike Fleming is an expert in industrial engineering and a recent graduate of Dartmouth. He now lives in Boston with his wife and 1 child. In his free time, he enjoys running and hiking. Mike has worked as an engineer for over 10 years, and has experience in a variety of industries.