What are some common uses for a 10 inch sliding miter saw?
Safety Tips for Using a 10-Inch Sliding Miter Saw
When using a 10-inch sliding miter saw, there are a few safety tips that should be followed. Firstly, always wear safety goggles and a proper respirator when cutting wood with a 10-inch sliding miter saw. Secondly, make sure the blade is properly sharpened and the saw is in good condition before using it. Finally, keep your fingers out of the blade when cutting and use a push stick to guide the board instead of your hand.
Cutting lumber and trim
Lumberjocks often debate the merits of different cutting methods, but few can deny that a 10 inch sliding miter saw is an incredibly versatile tool. With its wide range of motion and precise cuts, this saw can handle almost any task. Here I will discuss the benefits and drawbacks of using a sliding miter saw to cut lumber and trim.
The main advantage of using a sliding miter saw is its versatility. Unlike traditional hand-held saws, which are limited in terms of how much they can cut, a 10 inch sliding miter saw can handle virtually any size piece of lumber. This makes it perfect for tasks such as cutting boards, doors, windows, and even furniture legs.
The downside of using a sliding miter saw is that it is difficult to master the technique. Unless you have some experience using a saw blade in this manner, you may find it difficult to get accurate cuts. Additionally, because the blade moves so quickly across the wood surface, you may end up damaging the material if you are not careful.
Overall, a 10 inch sliding miter saw is an incredibly powerful tool that can be used for a variety of tasks related to lumber and trimming. However, care must be taken when using this equipment in order to avoid damage or mistakes.
Cutting pipes and tubing
One of the most common tasks a 10 inch sliding miter saw is used for is cutting pipes and tubing. This task can be difficult and dangerous if not done correctly.
When cutting pipes and tubing, it is important to use the correct tools and techniques. One of the most common mistakes people make when cutting these materials is using a incorrect saw blade or angle setting. By following these simple tips, you can ensure a safe and successful pipe cutting project:
-
Always use a quality 10 inch sliding miter saw. Make sure the saw is sharp and in good condition before starting any project.
-
When selecting a pipe or tubing cutter, make sure to choose one with a large enough blade to handle the thickness of your material. Try to avoid using angle cutters as they are not effective on thicker materials.
-
Use caution when making cuts as the blades on a 10 inch sliding miter saw are very sharp. Be aware of your surroundings at all times and keep proper safety precautions in mind when working with this tool.
Making precise cuts for molding and cabinetry
There are many different ways to make precise cuts with a 10 inch sliding miter saw. Here are two methods that you can use:
- Use a guide fence.
If you have a guide fence, simply attach it to the saw blade using screws or nails. Then, align the fence with the cutting edge of the blade and make your cuts. This method is easiest if you have a straight blade and if the plywood or other material you’re cutting is flat and rigid. However, if your material is curved or flexible, using a guide fence may not be practical because it will not keep your cut lines straight.
- Use a rip fence.
A rip fence is another type of guide that helps ensure accurate cuts by preventing wood from being ripped off when you make them. To use one, first measure the width of the material you’re cutting and buy an appropriate size rip fence (usually 3/8 inches to 1 inch wide). Then, attach it to one side of the saw table so that the teeth are aligned with the blade’s cutting edge. Make sure that the rip fence extends past both sides of the material so that it can be used as a stop when making your cuts.
Other Types of Miter Saws
There are a number of different types of miter saws, each with its own advantages and disadvantages. In this essay, we’ll take a look at some of the other types of miter saws and their uses.
Coping Saws
A coping saw is a type of miter saw that has a special blade designed for cutting curves along the edge of a workpiece. It’s commonly used for cutting out shapes like circles or stars. Because the blade is curved, it can cut more smoothly than a standard straight-edged saw blade, making coping saws great for cutting intricate curves and details.
Coping saws are often less powerful than standard miter saws, so they’re not ideal for cutting wide boards or large pieces of wood. They’re also not as versatile as standard miter saws, since they can only be used to cut curves. If you need to cut straight lines or cuts in flat surfaces, you’ll need to use a different type of miter saw.
Cabinet Saw
A cabinet saw is similar to a standard miter saw in that it has two sliding blades that allow it to make precise crosscuts on boards or timber up to 12 inches wide. But where a standard miter saw has an angle gauge on the side that allows you to set the angle of the blade relative to the board, a cabinet saw doesn’t have an angle gauge – instead, it has one or more rabbets (grooves) in the side rail that correspond to specific angles. When you slide the board into position under these rabbets, the cabinetsaw’s blades will automatically adjust to make the correct crosscut depth. This makes cabinet Saw perfect for precision work like fitting
Creating custom cuts for any project
When it comes to cutting projects with a 10 inch sliding miter saw, it is important to have the right cuts made. Custom cuts can be made for any project, and can make the job much easier. There are a few tips that will help when making custom cuts:
-
Use a jigsaw if possible. Jigsaws are great for making small, precise cuts. They are also easy to use and can be stored easily.
-
Check the dimensions of the project before beginning. Make sure that all measurements are correct before starting to cut. This will ensure that the final product is accurate and fits properly.
-
Be patient while making custom cuts. Taking your time and making sure each cut is perfect will result in a better final product.
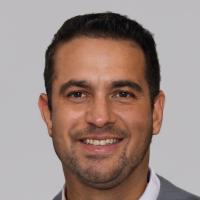
Mike Fleming
Mike Fleming is an expert in industrial engineering and a recent graduate of Dartmouth. He now lives in Boston with his wife and 1 child. In his free time, he enjoys running and hiking. Mike has worked as an engineer for over 10 years, and has experience in a variety of industries.